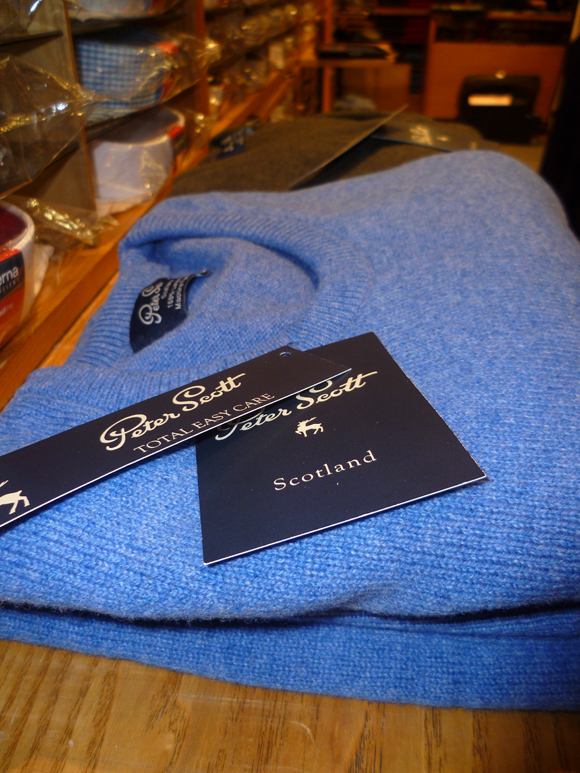
In 1878 in the small town of Hawick a change was happening in the knitwear industry. A young man by the name of Peter Scott bought a small unsuccessful knitwear mill, a risky acquisition by anyone’s standards due to the previous owner’s failure to make the business work, but as history demonstrates a risk worth taking.
With the right workforce, business acumen, skill and determination Peter Scott’s knitwear mill began to expand and by 1889 a new premise was required and the mill moved to its current location on Buccleuch Street, Hawick.
Originally branded as ‘Pesco’ the early days saw Peter Scott manufacture woollen underwear to protect against the harsh Scottish winters.
The process to produce a Peter Scott garment is long and painstaking and the garment must pass through many pairs of expert hands before it is allowed to pass into the hands of the customer. Although the knitting of the garment is carried out on machines many of the stages are done by hand and perhaps the most important of these are the meticulous inspections which each and every garment must pass prior to leaving the factory for sale. Any garment found to have even the slightest imperfection that cannot be mended back to a perfect state will be rejected as a second. These inspections coupled with the precision of the garment assembly and of course the all important washing, which is done in the softest Scottish water, add to the quality of the Peter Scott product at Robert Smart Menswear York.
Cost cutting is not an option and although time consuming, every single stage, and there are over 20, is recognised as being vitally important in the production of the ‘perfect’ Peter Scott piece of knitwear at Robert Smart Menswear York.
The process begins with the main panels (front, back and sleeves) being knitted on Frames or V Bed Shima. The panels are joined together across the shoulders and the sleeves are ‘set in’ or body linked. The sides of the garment and the sleeve lengths are then joined together (a process called seaming) and all running ends are made secure on a bar tacking machine. Next the garments are scoured (washed) and milled to the required finish or handle. They are then tumble dried and placed on a metal frame and steamed to size (Paris Press) which also removes any creases. The garment is then moved to the cutter who skillfully hand cuts the garment to the required style. The collars are linked to the garment or in the case of a cardigan the strapping will be stitched on using the plain stitch machine. The stitcher will add any pockets or zips and cardigans will have button holes made and buttons attached. All styles will then move on to the hand sew department where the finishing touches are completed by hand. The garment is checked for faults and passed to the final exam department where it is Hoffman pressed for presentation, tickets and labels are attached and it is folded and bagged ready for the customer.